Layers to Liftoff
How 3D Printing is Propelling Space Missions to New Heights (and the Challenges Ahead)
By Dora Strelkova
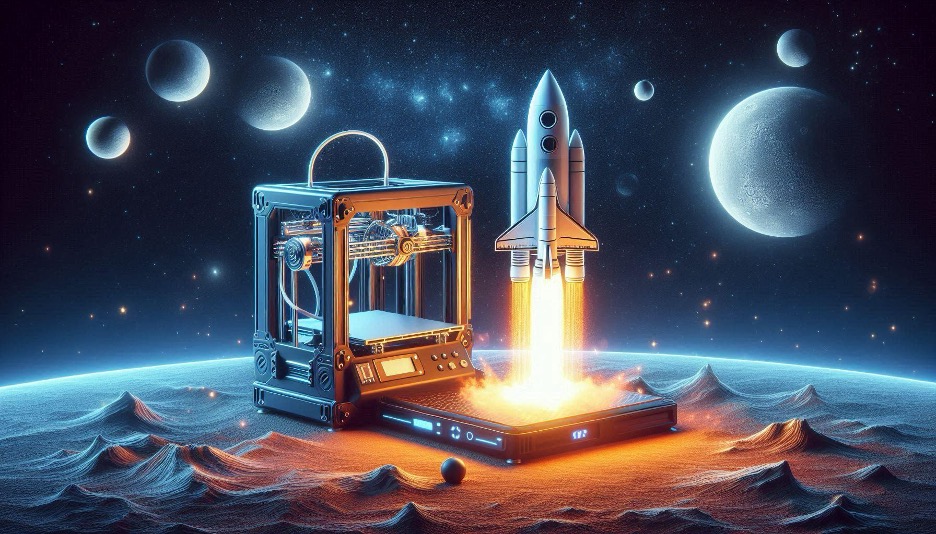
Created using Microsoft Bing Image Generator by the author.
Imagine a tool so versatile it could help you survive in one of the most extreme environments known to humankind—space. This tool could build your shelter, repair your equipment, and even provide you with sustenance in the form of specially crafted meals. It sounds like science fiction, but in reality, it’s a technology closer to our fingertips than ever before. This tool can turn an astronaut’s ideas into tangible, life-saving objects, layer by layer, in a home far from home.
While 3D printing (3DP) is often associated with trinkets produced by consumer-grade machines, its potential extends far beyond that. Desktop 3D printers are now common, affordable, and user-friendly, bringing the technology to everyday people. However, this is just the tip of the iceberg. In the industrial world, 3D printing—more accurately termed Additive Manufacturing (AM)—is a cutting-edge technology reshaping entire industries. According to the updated ISO/ASTM 52900 standard, there are seven distinct families of 3D printing processes, each using different techniques and materials [1].
Among these, the filament-based systems—familiar to many 3D-printer hobbyists—fall under “Material Extrusion.” In this process, materials are pushed through a nozzle to build objects layer by layer. This article explores three of these process families: Material Extrusion (MEX), Directed Energy Deposition (DED), and a Vat Photopolymerization (VP) variant. Each holds incredible potential for enabling survival in the harsh environment of space, giving explorers the tools to create sustainable habitats on Mars and perform critical in-situ repairs. Imagine a future where astronauts aren’t just explorers but creators—building the devices, structures, and even food needed to thrive in space.
3D Printing Food with Material Extrusion (MEX)
As NASA and the Canadian Space Agency (CSA) prepare for long-duration missions to the Moon, Mars, and beyond, projects like BeeHex are exploring 3D printing food in space. This technology uses the material extrusion (MEX) process, where food is built layer by layer using gel-like materials extruded through syringe-like nozzles. The goal is to preserve the freshness, nutrient profile, and taste of meals, allowing astronauts to enjoy nutritious food while far from home [2]. Pre-packaged foods often lose nutritional value over time, making them inadequate for multi-year journeys to Mars. 3D printing offers a solution by enabling personalised meals tailored to astronauts’ dietary needs [3].
Since the inception of the BeeHex project (American development), the 3D-printed food industry has expanded significantly, with ongoing Canadian research into edible creations [4]. These printers excel at crafting intricate food structures, but many do not actually cook the food. Companies like Steakholder Foods and Revo Foods are exploring 3D-printed meats and plant-based fish fillets, which offers the potential of bringing printed proteins to space [5][6].
However, challenges remain. The stability of printing gels in microgravity, logistics of storing and rehydrating food components, and the time-consuming nature of the printing process must be addressed. Additionally, limited availability of materials and higher costs pose obstacles. Nonetheless, the ability to produce personalised meals on demand could revolutionise how we nourish astronauts, turning mealtime into a delightful experience rather than a chore.
In-Situ Repair with Directed Energy Deposition (DED)
As space missions become more ambitious and prolonged, the need for efficient in-situ repair solutions is paramount. Two promising technologies, Berkeley’s Computational Axial Lithography (CAL) and Directed Energy Deposition (DED), hold the potential to revolutionise how astronauts address equipment malfunctions in the unforgiving environment of space.
CAL is revolutionizing AM with its unique approach. This innovative process, a modified form of Vat Photopolymerization (VP), uses light to transform a viscous liquid into solid objects at incredible speeds—sometimes in as little as 20 seconds [9]. This capability is crucial for astronauts, enabling them to rapidly produce replacement parts and tools on demand, significantly reducing the need to carry extensive inventories of spare components on long-duration missions.
CAL’s potential extends beyond mechanical repairs; it can also address the medical needs of crew members. Imagine printing dental implants, skin grafts, or custom lenses right on board—a game changer for emergency medicine in space [9]. This technology not only promises to enhance mission efficiency but also safeguards astronauts’ health and well-being, making it an indispensable asset for future exploration. Researchers at Berkeley have already begun testing this technology in space, showcasing its promise as a vital tool for future missions [9].
DED is already used on Earth to repair metal components, extending their life cycles. For instance, Prima Additive employs DED technology to fix turbine blades, demonstrating its effectiveness in extending the life cycle of a part [11]. This technique involves using a laser to melt and deposit wire metal material, a potential for maintaining essential systems in space? However, the behaviour of a laser in the vacuum of space could introduce unpredictable variables, necessitating an enclosed DED system to ensure controlled operation and safety. Programming tools like APlus, developed by CAMufacturing Solutions Inc., are instrumental in the programming of DED processes, allowing for precise control and efficient repairs [12].
Several questions must be addressed to realise the potential of DED for in-situ repairs in space. For example, how will repair materials be stored and transported aboard a spacecraft, and what contingency plans exist if material supplies run low? Additionally, the feasibility of 3D scanning in microgravity poses a significant challenge. If a component requires repair, can astronauts scan it and send the data back to Earth for toolpath generation? Finally, mounting tools for repairs presents dilemmas. Would it be necessary to remove a metal part from its assembly to repair it, or could repairs be executed while the component remains in place? This is particularly challenging due to heat dissipation concerns that could affect surrounding components.
Printing Infrastructure with Material Extrusion (MEX)
3D-printed infrastructure is set to redefine how we establish human habitats beyond the concrete creations on Earth. Researchers in Canada are pioneering the use of extraterrestrial materials, like lunar and Martian soil, to construct livable structures far from home [13]. University of Western and York Engineers Jun Yang and Zheng Hong (George) Zhu are at the forefront of this innovation, utilizing a vacuum chamber that houses both a 3D printer and an AI-enhanced robot for experimentation [13]. This setup allows them to tackle critical challenges such as layer bonding and heat buildup, ensuring that the printed structures can withstand the harsh environments of other planets.
However, several obstacles remain. Adapting 3D printer hardware for space travel is crucial, as is selecting optimal additives for mixing with extraterrestrial soil. Researchers must also consider how to efficiently collect and prepare the soil for the printing process. Notably, a 2018 PhD thesis by Christopher Chan from the University of Waterloo examined the potential of 3D printing a Mars research station, further highlighting the feasibility of this ambitious vision [14].
Promisingly, on July 6th of this year, a Mars crew successfully completed a 378-day simulated NASA mission, living and working in a 158-square-metre 3D-printed habitat known as the Mars Dune Alpha [15]. The mission was designed to support human health and performance research, helping to pave the way for future expeditions to Mars [15].
Mars Dune Alpha was 3D-printed at the Johnson Space Center in Houston using ICON’s Vulcan system and their proprietary mortar-based concrete, Lavacrete, which was dyed red [16]. This fully enclosed 3D-printed habitat is the first of its kind to be used for space research [16].
The implications of 3D printing habitats are revolutionary, as it promises to create adaptable living spaces tailored to the unique conditions of other planets. By leveraging local resources, we can build sustainable infrastructures that enable humanity to thrive in these new frontiers, taking a significant leap toward our goals of deep space exploration and colonisation.
General Challenges with 3D Printing in Space
Regardless of the 3D printing process, challenges arise when considering the transition from printing on Earth to the unpredictable environment of space. What happens if a printer breaks or malfunctions? Will the crew need to be trained to repair and operate each system, effectively assuming the roles of application engineers and service technicians? This situation raises important questions about the technical expertise astronauts must possess to ensure the seamless operation of 3D printing systems.
Another significant challenge lies in miniaturisation. How can 3D printers be designed to be lightweight and compact enough for a space shuttle? It is also crucial to consider whether these systems can be assembled from sub-models in space, thereby eliminating the need to transport bulky tools for assembly. We should also explore the idea of deploying AM autonomously, sending it to the destination planet prior to a crew’s arrival [16].
Power supply management is another critical concern. 3D printers require a consistent and reliable energy source. For systems used to build infrastructure on other planets, solar power through photovoltaic arrays or variations of the Multi-Mission Radioisotope Thermoelectric Generator (MMRTG) currently employed by the Mars Curiosity Rover, could be explored [17] [18]. Ensuring these systems operate effectively in space’s unique conditions is essential for functionality.
Material stock poses another challenge: how much printing material should be brought aboard? This question is vital for ensuring astronauts have sufficient resources while minimizing excess weight. Finally, transferring files to the spacecraft presents a communication hurdle. Given the long distances involved, will astronauts have the necessary computer-aided design (CAD) skills in space, and should they be expected to create or modify designs on their own? Addressing these challenges is crucial for leveraging the full potential of 3D printing technology in space exploration. Please note, this article outlines some possible challenges, but definitely not all of them.
Concluding Remarks
Today, 3D printing technology stands on the Slope of Enlightenment, as researchers and engineers move beyond early hype to realise its practical applications in space exploration [19]. While the road ahead is full of technical challenges, 3D printing is steadily proving its potential as a critical survival tool for humanity’s future in space, propelling us toward a new era of exploration and innovation.
Even with the optimism surrounding the adaptation of this technology for unique applications, many hurdles remain in the adoption and design processes.
References
[1] https://www.additivemanufacturing.media/cdn/cms/7_families_print_version.pdf
[2] https://spinoff.nasa.gov/Spinoff2019/ip_2.html
[4] https://www.ualberta.ca/en/folio/2024/06/3d-printing-heats-up-food-safety.html
[5] https://www.steakholderfoods.com/blog/3d-printed-meat
[6] https://revo-foods.com/what-in-the-world-is-3d-food-printing/
[7] https://www.youtube.com/watch?v=0I_gJbyXC5I
[8] https://www.cbc.ca/radio/thecurrent/3d-printed-fish-fillet-1.6867095
[9] https://engineering.berkeley.edu/news/2024/07/berkeley-researchers-send-3d-printer-into-space/
[10] https://www.sciencedirect.com/science/article/pii/S0094576523003478#fig6
[11] https://www.primaadditive.com/en/stories/direct-energy-deposition-keeps-circular-economy-spinning?
[12] https://camufacturing.com/
[13] https://news.westernu.ca/2021/03/3d-printing-in-space/
[14] https://uwspace.uwaterloo.ca/items/5d159de1-9c1a-444c-b049-fdf5351d9148
[17] https://ntrs.nasa.gov/api/citations/20040191326/downloads/20040191326.pdf
[18] https://mars.nasa.gov/internal_resources/788/
[19] https://www.gartner.com/en/research/methodologies/gartner-hype-cycle
About the authors:
About the authors:
About the authors
Dora Strelkova is a Mechanical Engineering graduate student and previous Software Developer at CAMufacturing Solutions Inc., a company that focuses on Additive Manufacturing (AM) toolpath programming for hybrid processes, particularly for Directed Energy Deposition (DED). Her current research explores the integration of compliant mechanisms and origami in the design of robot end effectors.
With prior experience as an AM Lab Technician, Dora has acquired industry expertise in processes such as DLP, FDM, and DMLM, gained through hands-on work with Stratasys and GE Concept Laser systems. She holds the TBGA AM Certificate for Engineers and Managers from Purdue University and has developed proficiency with desktop additive machines through her personal projects in film props and fashion-related AM production. She is also a Certified Additive Manufacturing Technician (CAMT) through SME.
YouTube (@strelkomania): https://www.youtube.com/@strelkomania